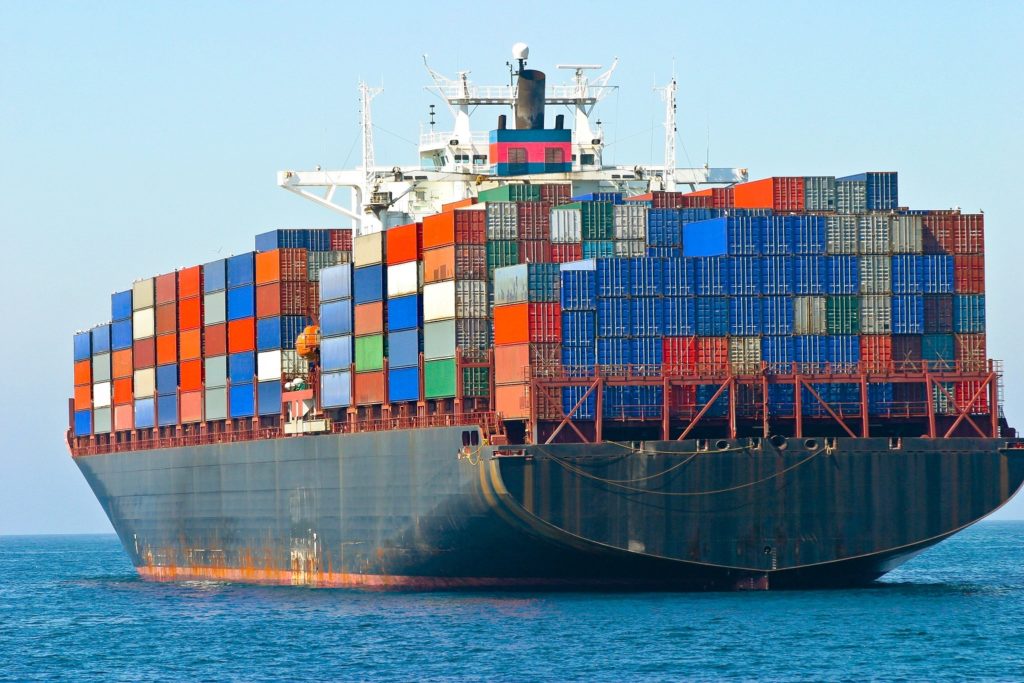
Seems like most industries have a tangled supply chain. The entire transportation system is sorely distressed.
The elitists in federal and state governments have a staggering level of hubris. They think waving their hands, clicking on their laptops, issuing press releases will make the entire economy bend to their will. What they accomplish is willfully causing disruption in your life and in my life.
Here are merely a few of the recent articles describing the tangled impact of Covid dictats and sundry government policies:
- Lots of cargo ships are waiting to unload off the California coast.
- Large port operator expects disruptions to last into 2023.
- Workers in transportation sector warn of possible system collapse.
- Chip shortage for carmakers will last into late 2022.
Looks like it might take another 15 or 18 months to untangle the worldwide supply chain.
Wall Street Journal – 8/17/21 – Cargo Ships Are Again Idling Off Jammed Southern California Ports – Back in the middle of August the tally of cargo ships sitting off to coast of California was 37.
A tweet I saw this morning (10/9/21) from someone flying out of Long Beach indicated the individual counted 50 ships waiting to unload.
At around 10,000 containers per ship that is somewhere around 370,000 containers waiting to be unloaded back in the middle of August and is now currently somewhere in the range of half a million containers sitting off the coast.
Article says a few months ago it was only nine. Normally it is zero.
I read another article a couple weeks back saying there are 200 ships waiting off the coast of Chinese ports waiting to pick up cargo. Ship captains don’t sit around waiting to get loads. That means there is somewhere around two million containers waiting to be shipped. Didn’t bother to find a link for that article.
Update 10/11/21 – WKRN – 10/10/21 – Major cargo backup could leave holiday shelves bare – Article says there are 146 cargo ships either anchored offshore or in port at the two Southern California ports of Long Beach and Los Angeles. That is a record number of backup. Article above says usually there are zero ships waiting to get offloaded.
The supply chain backlog is not just ships waiting to get offloaded. There are restrictions on how fast containers can be offloaded. There are space constraints on how many more containers can be stored at the docks waiting for a truck. There are restrictions on how many trucks can get through the yard and how fast containers can get loaded on railroad cars. There even potential constraints of containers sitting on the dock they can’t get back to where they can be filled.
Article says 76 of the backlog ships have clothes, furniture, and electronics. Those 76 have been stalled for three months. Article says each one of them is carrying 14,000 containers with something in the range of $100,000 of inventory.
Let’s do some math. If each ship has 14,000 containers with each of them worth $100,000, then they carry $1.4 billion of inventory. Multiply that merely by the 76 which are carrying clothes, furniture, and electronics brings us to $106 billion of merchandise.
If all 146 ships are caring that much stuff the value of backlog is $204 billion.
Article says Walmart, Target, Home Depot, Costco, and other retailers are chartering their own ships in an effort to expedite delivery. Great idea, however, their privately chartered ships will go to the back of the 146-ship long line off Southern California.
The Epoch Times – 10/4/21 – One of World Largest Port Operators Warns Global Supply Chain “Crisis” Will Last Longer Than Expected – (I would link to the original source of this reported article except the subscription price is $415 a year. Um, not.) Dubia DP operate ports across Africa, the Americas and in India, Russia, and Europe. Article says they are one of the largest operators of ports and cargo facilities in the world.
The chairman and CEO of the company says transportation bottlenecks are going to continue until 2023. This is going to have ongoing impact on costs. (Another article I’ll mention soon says the costs for a 40 foot container from China to the US has risen from about $1,400 before the pandemic to about $20,000 today.)
The executive says that in ports across Asia when there is “an incident” of Covid the entire port is shutdown. He indicates some manufacturers are looking at three-year delay in production because they cannot get components.
Article cites several comments from the biggest shipping company in the world that the supply bottlenecks are going to run longer than expected. No indication in the article of what the expectations were or how long the shipper expects the bottlenecks to continue.
The Epoch Times – 9/29/21 – Workers Who Maintain Supply Chains Warn of Worldwide “System Collapse” – Four trade associations and unions, who assert they represent 65 million workers in the transportation industry around the world, issued a warning to the UN General Assembly and its members that the worldwide transport system is beginning to buckle under two years of strain from Covid restrictions. Shortages of workers and poor treatment of existing staff is increasing pressure on transportation.
The groups are asking governments to reduce the Covid restrictions and quarantines which are restricting transportation. There warning of a “global transport system collapse” because of the strain on workers.
Daniel Yergin and Matteo Fini at Wall Street Journal – 9/22/21 – For Auto Makers, the Chip Famine Will Persist – For a product has thousands or tens of thousands of parts that go into assembly, when the supply chain gets tangled up industrywide for one component the entire production cycle industry-wide gets tangled. Merely one example is the small computer chips that go into a modern car.
Article says production of cars has fallen 7 million short of where the market should be. Toyota cut production 40% in September.
Inventory of new and used cars is scarce.
A typical new car now requires something in the range of 1000 computer chips for everything from window control, to air-conditioning settings, and adaptive cruise control.
Number of chip producers has dropped over the years. Infections have disrupted the remaining plants. Specific issues have hit other plants, such as a drought in Taiwan, fire at one Japanese plant, and a storm shutting down producers in Texas.
Authors’ company predicts it will be well into late 2022 before production catches up with demand. With Daniel Yergin making that estimate, you might want to make appropriate plans.
God observations and quite predictable. I wrote to the President back in 2020 that as we were creating task forces to develop and distribute vaccines and medical materials to address the pandemic, we should have another task force focused on identifying the discontinuities in the economy that would result from the pandemic and closure of so many activities. The US has an aversion to doing anything like economic planning, perhaps because it smacks of the centrally managed economy of the Soviet state that was such a failure. But the unwillingness to use their resources to help the plight of citizens is frustrating.
Certainly the federal and state government could have figured out solutions to clearing the port in LA. Certainly the critical materials for certain kinds of production could have been identified and some enhancement to the regulations, exceptions, etc. could have been arranged. Even more recently the shortage of baby formula was a direct result of government action. The FDA shut down the major plant, creating a severe shortage, hoarding, etc. Yet they did nothing to assist the company in resolving the issue. There are too many such examples to attempt to itemize.
It is a matter of policy not to do such things. Neither party is responsible; both are at fault. Solutions by pronouncement are not any kind of an answer.
Hi John:
Thanks for your comment. My apologies for the tardy clearing of the comment. I’ve been somewhat distracted with our move.
Jim